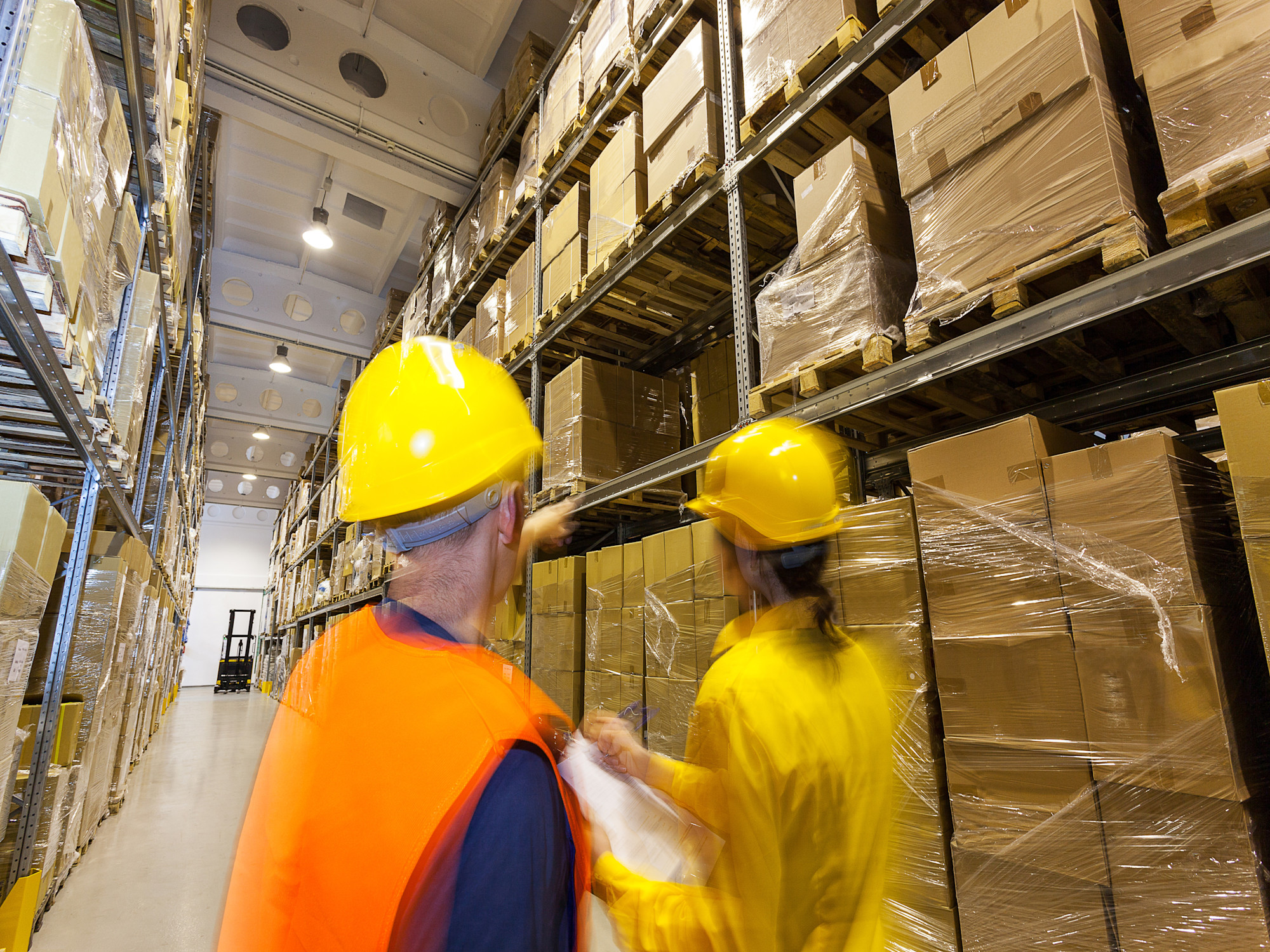
Diseño y Distribución de Instalaciones de DSM
Comenzando Fuerte: La Base del Diseño Efectivo de Distribución de Instalaciones
La configuración inicial de los sistemas de producción debe tener en cuenta todos los factores relevantes para garantizar el éxito a largo plazo. Una distribución de instalaciones cuidadosamente planificada mejora las operaciones y evita interrupciones innecesarias.
Ajustar las distribuciones después de que la producción haya comenzado puede llevar a tiempos de inactividad costosos y la pérdida potencial de clientes. Al aprovechar conocimientos operativos clave, nuestro equipo de consultoría de ingeniería desarrolla distribuciones optimizadas adaptadas al flujo de trabajo de su empresa, asegurando la eficiencia y minimizando los desafíos futuros.
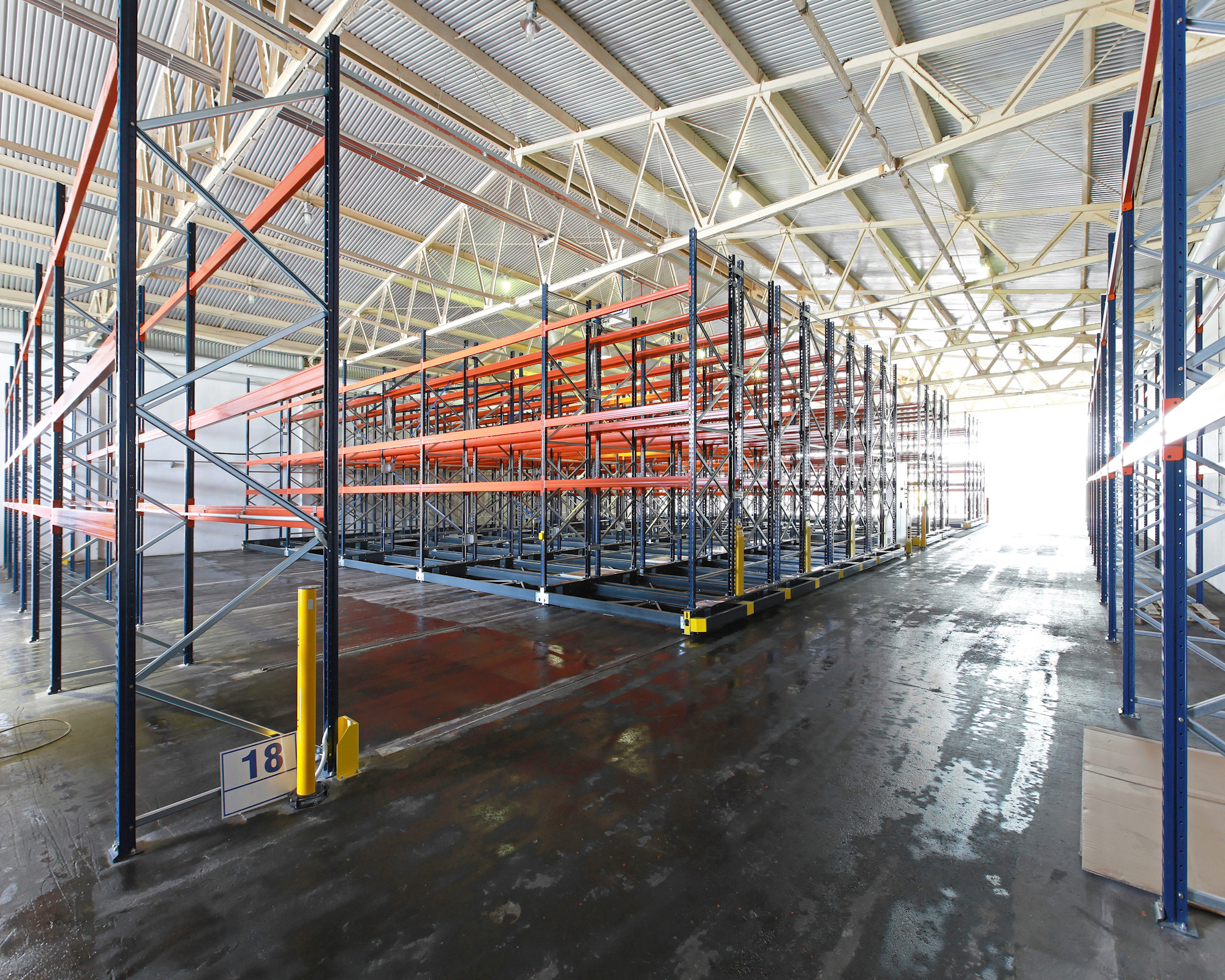
Consideraciones para el Diseño y Distribución de Instalaciones de DSM
Factores Clave en el Diseño de Instalaciones
Una distribución efectiva de una instalación de manufactura equilibra las necesidades de los trabajadores, materiales y equipos para crear un sistema funcional que mejore la productividad y asegure una salida de alta calidad. Aquí están las consideraciones esenciales para diseñar una distribución optimizada:
Comunicación:
El diseño debe facilitar una comunicación clara y una supervisión eficiente.
Bienestar del Empleado:
Una distribución que mejora el ánimo y la motivación contribuye a una fuerza laboral más comprometida.
Flujo de Proceso:
Los materiales deben moverse sin problemas a través de la instalación sin demoras ni cuellos de botella.
Seguridad:
Asegurar que todas las operaciones cumplan con las regulaciones locales y los estándares de seguridad federales.
Utilización del Espacio:
El diseño debe asignar espacio adecuado para almacenamiento, preparación y movimiento fluido de materiales, empleados y equipos.
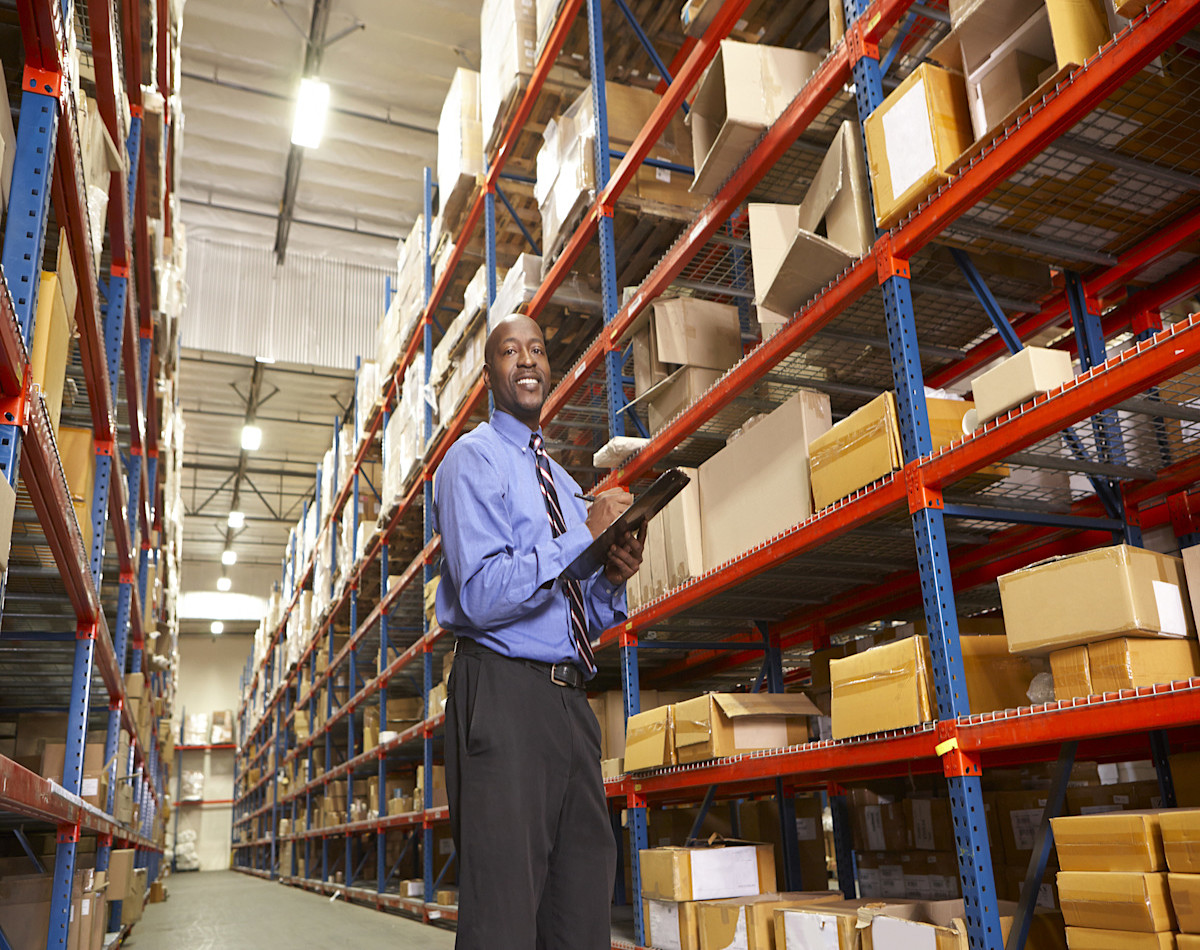
Principios de Manufactura Esbelta en el Diseño y Distribución de Instalaciones de DSM
Principios de Manufactura Esbelta en el Diseño de Distribución de Instalaciones
Diseñar un sistema de manufactura esbelta implica alcanzar objetivos específicos que mejoran la eficiencia y la productividad. Evaluando los roles y responsabilidades del personal, las organizaciones pueden aumentar la moral, utilizar mejor las habilidades de los empleados y optimizar la salida.
La racionalización de los sistemas de producción minimiza los tiempos de espera improductivos, reduce el exceso de inventario y elimina los movimientos innecesarios dentro de la instalación. Estos principios forman la base de una distribución óptima de una instalación esbelta, proporcionando estos beneficios clave:
Mejora de la Moral del Empleado:
Reducir tareas repetitivas y actividades no productivas lleva a una mayor satisfacción laboral.
Tiempos de Plomo Más Cortos:
Las operaciones optimizadas permiten una respuesta más rápida y una mejor adaptabilidad a las demandas cambiantes.
Márgenes de Beneficio Mayores:
Las mejoras en la eficiencia a lo largo del ciclo de producción impactan positivamente en los resultados económicos.
Mejora de la Calidad del Producto:
Los procesos optimizados mejoran la precisión y fortalecen las medidas de control de calidad.
Reducción de Desperdicios:
Eliminar ineficiencias reduce los desperdicios y aumenta el ahorro de costos.
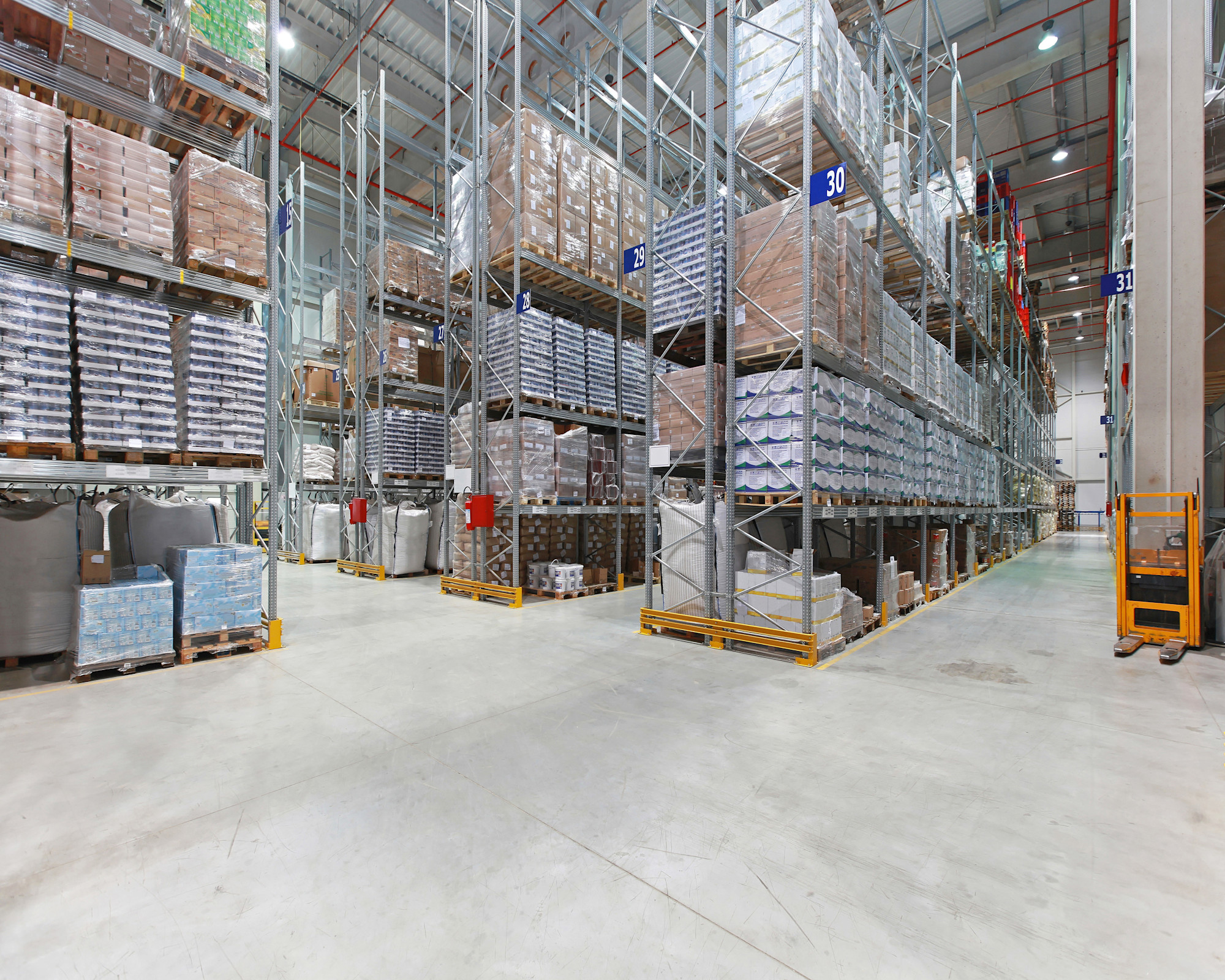
Diseño y Distribución de Instalaciones de DSM: Escaneo Láser 3D
Transforma el Diseño y Distribución de Instalaciones con el Escaneo Láser 3D
El escaneo láser 3D revoluciona el diseño de instalaciones al proporcionar a arquitectos, ingenieros y gerentes un nivel de precisión y detalle sin precedentes sobre los espacios existentes. Utilizando tecnología de vanguardia, se capturan rápidamente millones de mediciones precisas, creando un modelo 3D altamente detallado—un gemelo digital—de tu instalación.
Este gemelo digital te permite visualizar tu instalación en 3D, habilitando decisiones basadas en datos, reduciendo errores costosos y optimizando flujos de trabajo. Al aprovechar esta tecnología, puedes mejorar la seguridad, maximizar la eficiencia del espacio e integrar sin problemas nuevos equipos—todo antes de realizar cualquier cambio físico.
Con nuestros servicios de escaneo láser 3D, puedes planificar y ejecutar la distribución de instalaciones con confianza, minimizando el retrabajo en sitio y mejorando la productividad mientras aprovechas al máximo tu espacio disponible.